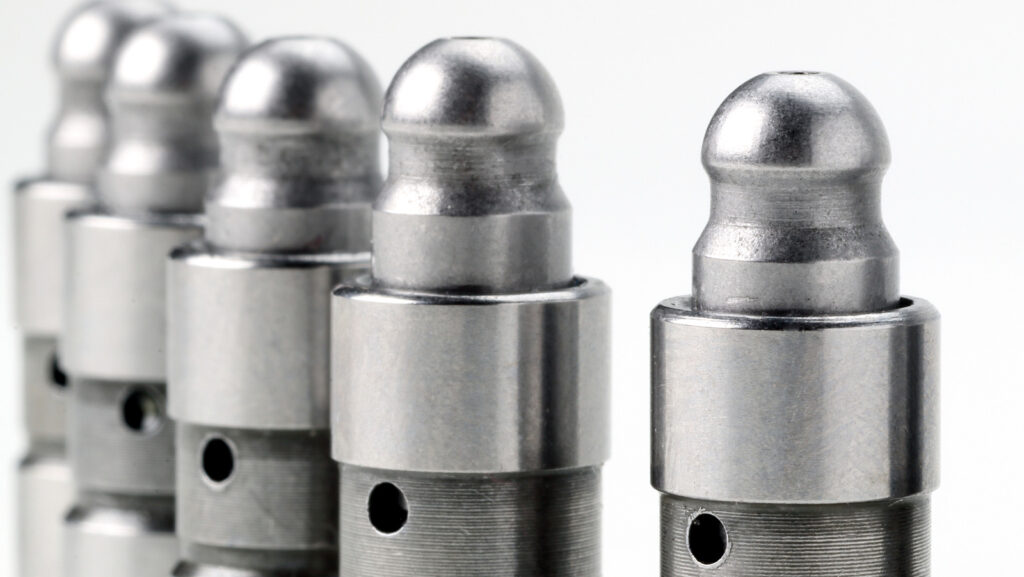
In the evolution of automotive engineering, the transition from solid lifters to hydraulic lifters marks a significant shift in engine design. Solid lifters, once a staple in high-performance and everyday vehicles, have been largely replaced by hydraulic alternatives due to advancements in technology and changing consumer demands.
Solid lifters excel at transferring energy from a cam lobe or rocker arm, primarily because they are essentially solid metal cylinders. These components can either be flat, relying on lubrication to prevent wear, or equipped with rollers to reduce friction and allow for higher RPMs. However, solid lifters require precise lash settings to maintain optimal valve travel, a task complicated by thermal expansion and constant mechanical stress.
The Rise and Fall of Solid Lifters
The decline of solid lifters in modern vehicles is not due to a lack of capability but rather to the demands of maintenance and reliability. While advances in metallurgy and design have extended the lifespan of solid-lifter engines, they still require regular adjustments. For instance, the M110 inline-6 engine in 1970s and 1980s Mercedes 280Es needed valve adjustments every 10,000 miles. In today’s market, where convenience is key, such frequent maintenance is impractical.
According to industry experts, car manufacturers prioritize components that require minimal maintenance. This preference is evident in the widespread adoption of “lifetime transmission fluids” in sealed transmissions, despite skepticism about their longevity. The shift away from solid lifters aligns with this trend, as consumers increasingly expect vehicles to be low-maintenance.
The Advantages of Hydraulic Lifters
Hydraulic lifters, although heavier and more complex than their solid counterparts, offer significant advantages. They feature small pistons that use oil pressure to transfer energy from the cam to the valve, eliminating the need for manual adjustments. This design effectively nullifies component wear by preventing thermal expansion from disrupting precision-set lash.
The cushioning effect and additional weight of hydraulic lifters do limit RPM and response slightly, but not to a degree that affects 99% of driving conditions. For most drivers, the trade-off between performance and convenience is well worth it.
Implications for the Automotive Industry
The transition to hydraulic lifters reflects broader trends in the automotive industry, where reliability and ease of use are paramount. As vehicles become more sophisticated, the expectation for components that require little to no maintenance continues to grow.
Looking forward, it’s unlikely that solid lifters will make a significant comeback in mainstream vehicles. They may still find a place in niche markets, such as track-focused models, where performance takes precedence over convenience. However, for the average consumer, hydraulic lifters represent the ideal balance of performance, reliability, and maintenance ease.
In conclusion, the abandonment of solid lifters in favor of hydraulic alternatives underscores the automotive industry’s commitment to innovation and consumer satisfaction. As technology advances, we can expect further developments that enhance vehicle performance while minimizing the burden of upkeep.